Trickling
The Trickling Impregnation method is regarded as the most effective system for impregnating electrical windings. The resin is applied by dripping, keeping the stator rotating and positioning the product in specific points where is needed. The result is a perfectly impregnated winding without contamination of packed surfaces.
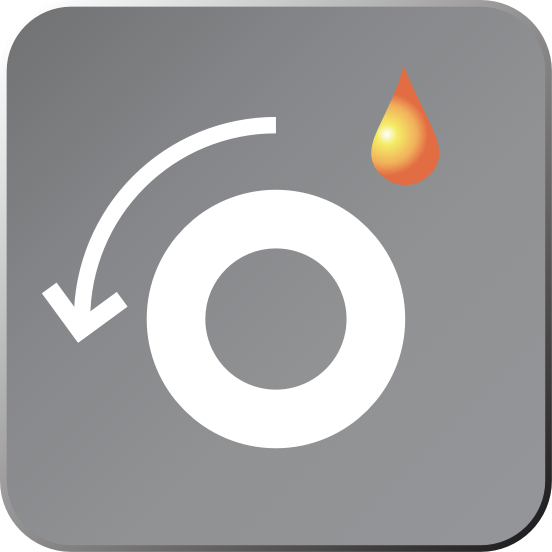